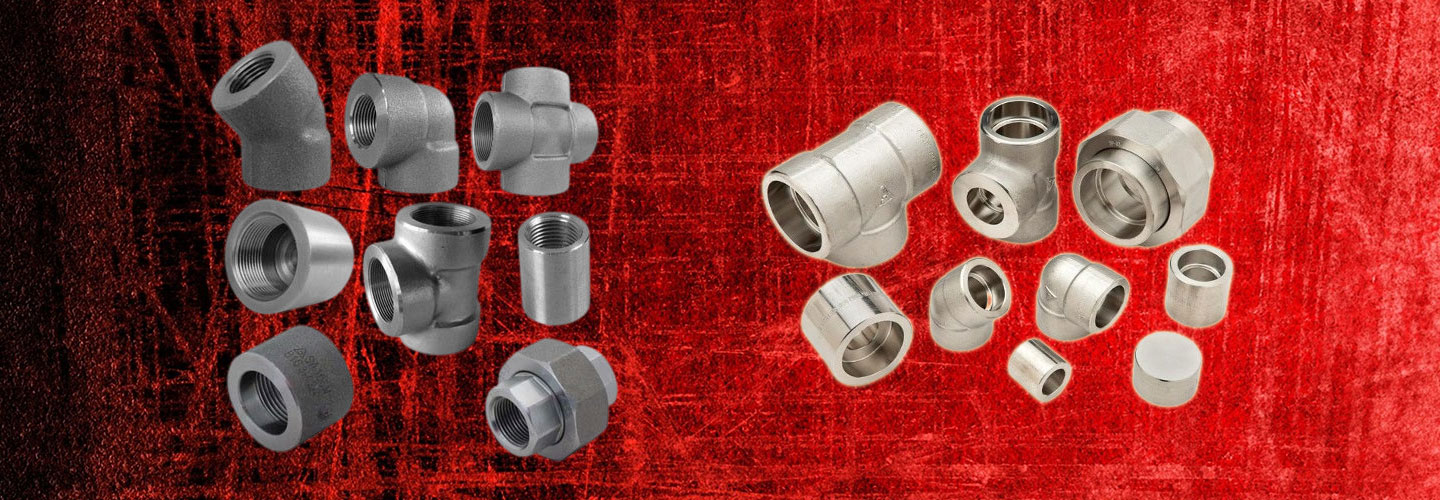
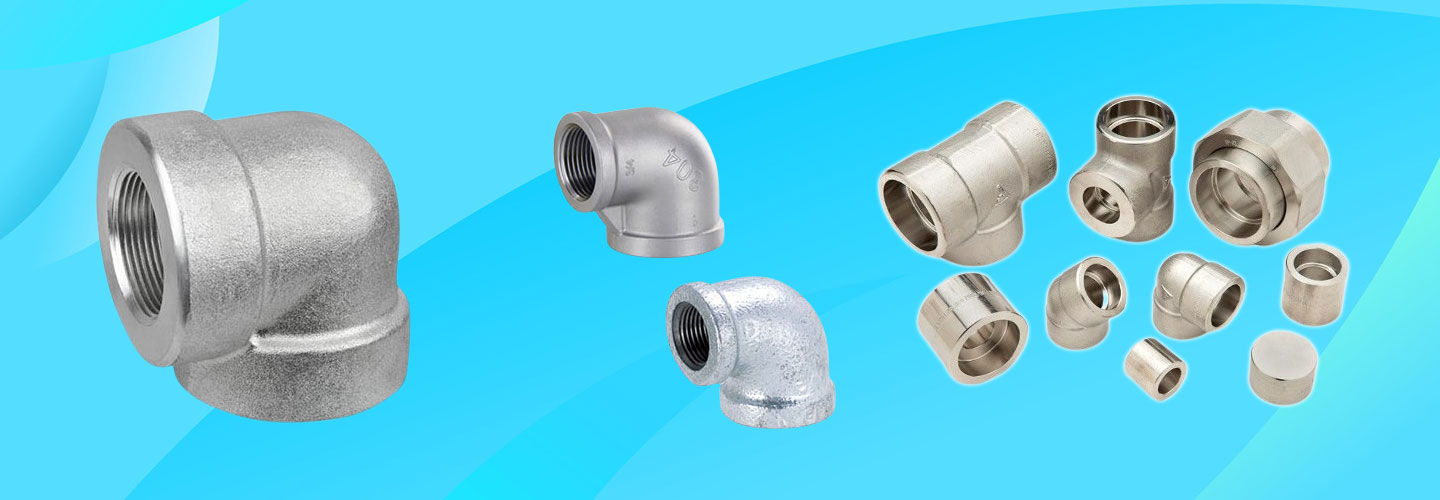
Socket Weld Fittings Manufacturer
Home / Socket Weld Fittings

What is Socket Weld Pipe Fittings?
A Socket Weld Fitting is a type of pipe attachment detail where the pipe is inserted into a recessed area of a fitting, valve, or flange. To join the pipes or valves to other sections of the pipe, fillet-type seal welds are applied. Socket Weld Fittings are a good choice in certain cases due to their advantages of strong structural strength and high leakage integrity. These factors are important considerations when designing a pipeline project.
How to describe socket weld pipe fittings dimensions correctly?
When placing a request for Socket Weld Fittings, it is important to specify the OD (outside diameter) dimensions and the pressure requirements (or thickness schedule). Socket weld fittings have pressure ratings that are typically expressed in class 3000, class 6000, and class 9000.
Socket weld pipe fittings are usually simplified as SW pipe fittings, so you will see some descriptions like SW elbow, SW tees, SW couplings etc.

Usage about socket weld fittings
Due to their high-pressure capabilities, socket weld fittings are commonly used in a wide range of industrial processes.
- Socket weld pipe fittings, such as elbows, tees, and reducers, can be used in pipelines to convey toxic, flammable, or expensive materials where leakage is not acceptable.
- Used in conjunction with ASME pipes to facilitate changes in dimensions.
- Applied in situations where the pipe work is considered to be permanent. They are designed in a way that provides good flow characteristics.
- Manufactured in accordance with ASTM A234 standards and can also confirm to ASME B16.11. This is a standard that covers dimensions, pressure-temperature ratings, marking, tolerances, and requirements for materials for carbon steel and forged carbon. In terms of acceptable material forms, they include bars, forgings, seamless tubes, and seamless pipes which conform to the requirements of fittings chemicals, mechanical property, and practices.
Socket Weld Advantages and Disadvantages
Advantages
- The pipe needs to be bevelled in preparation for welding.
- Temporary tack welding is generally not required for alignment because the principles in fitting ensure proper alignment.
- The socket weld metal is unable to penetrate the bore of the pipe.
- Construction costs have been found to be lower than those of butt-welded joints due to the elimination of special machines and the lack of exact fit-up requirements.
Disadvantages
- The welder should ensure that the expansion gap between the socket shoulder and the pipe is 1.6mm.
- The presence of internal crevices and expansion gaps in socket weld systems can promote corrosion. As a result, they are considered less suitable for radioactive or corrosive applications.
- These types of fittings are also not suitable for Ultra High Hydrostatic Pressure in food industries. This is because, in addition to not allowing full penetration, they also leave crevices and gaps that are difficult to clean.
Quick Links
- Nippolet Pipe Fittings Manufacturer
- Latrolet Manufacturer
- Threadolet Manufacturer
- Sockolet Manufacturer
- Sweepolet Manufacturer
- Nipolet Manufacturer
- Elbolet Manufacturer
- Weldolet Manufacturer
- Pipe Bushing Manufacturer
- Socket Weld Fittings Manufacturer
- Pipe Fittings Plug Manufacturer
- Pipe Fittings Plug Manufacturer
- Bronze Pipe Fittings Manufacturer
- Stainless Steel Pipe Fittings Manufacturer
- Weldolet Pipe Fittings Manufacturer
- Sockolet Pipe Fittings Manufacturer
- Forged Fittings Manufacturer
- Union Pipe Fittings Manufacturer
- Reducing Pipe Fittings Manufacturer
- Long Screw Pipe Fittings Manufacturer
- Jumnut Pipe Fittings Manufacturer
- Hose Connector Pipe Fittings Manufacturer
- Cross Pipe Fittings Manufacturer
- Boiler Mounting & Pipe Fitting Manufacturer
- Bell Mouth Pipe Fittings Manufacturer
- Tube Fittings Manufacturer
- Alloy Steel Pipe Fittings Manufacturer
- Carbon Steel Pipe Fittings Manufacturer
- Mild Steel Pipe Fittings Manufacturer
- Gi Pipe Fittings Manufacturer
- Branch Outlets Manufacturer
- Buttweld Fittings Manufacturer